Galvanoplastia de zinc
Elija el mejor proceso para su operación.
El zinc y sus aleaciones se han utilizado durante más de 100 años como recubrimientos protectores y decorativos sobre una variedad de sustratos metálicos, principalmente el acero. A lo largo de los años, se han desarrollado varios procesos para aplicar recubrimientos de zinc. La elección depende del sustrato, los requisitos de recubrimiento y el costo. Entre éstos, la galvanoplastia es el más frecuente para aplicaciones funcionales y decorativas.
Cuando se escoge un proceso de galvanoplastia de zinc, es importante saber qué procesos están disponibles y cada una de sus ventajas y desventajas particulares. La Tabla 1 compara algunos de los factores más importantes relacionados con estos procesos.
Contenido destacado
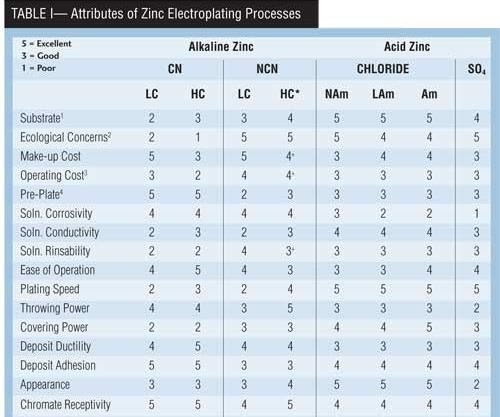
Tabla I. Atributos del proceso de galvanizado de zinc.
Factores a considerar
A continuación, se listan, en orden de importancia, los principales factores que deben considerarse al elegir un proceso de galvanoplastia de zinc:
- ¿Las especificaciones de revestimiento para la pieza requieren un depósito de zinc o de aleación de zinc?
- ¿Sustrato(s) a ser revestido?
- ¿Se requiere protección contra la corrosión?
- ¿Se requiere uniformidad en el espesor del depósito?
Teniendo en cuenta estas preguntas, se debería reducir el número de procesos de galvanoplastia a utilizar. El siguiente paso es considerar los factores secundarios. Estos factores se presentan a continuación y varían de un taller a otro:
- Características del depósito (aspecto, ductilidad, adherencia, etc.).
- Costos de producción y operación.
- Factores de operación (eficiencia, requisitos de pregalvanizado, corrosividad, etc.)
- Restricciones ambientales (calidad del aire, remoción de metales pesados, amoníaco, etc.)
Después de evaluar completamente cómo estos factores afectan sus circunstancias, las opciones del proceso qué mejor aplica deben reducirse considerablemente. A continuación, se presenta información específica que desglosa cada uno de los diferentes procesos de galvanoplastia de zinc.
Galvanoplastia de zinc cianurado alcalino
Durante mucho tiempo, la galvanoplastia de zinc cianurado fue el caballo de batalla de la industria, aunque su popularidad ha disminuido significativamente con el paso de los años en Estados Unidos y otros países. El uso del zinc cianurado continuará decreciendo a medida que los profesionales de acabados de superficies busquen reducir el manejo de desechos y por la preocupación sobre la clasificación de residuos peligrosos. También se busca eliminar la exposición de los trabajadores y la presión normativa sobre el uso de cianuro. Los requisitos operativos para un proceso de galvanoplastia de zinc cianurado son mínimos en comparación con los otros procesos de galvanoplastia de zinc. El análisis del baño, las pruebas de celdas Hull y otras pruebas de galvanoplastia, deben realizarse semanalmente. Los requisitos de limpieza y decapado no son muy estrictos, pero deben corregirse si existe un problema evidente de preparación.
Conformación del baño. Hay dos opciones disponibles para la conformación del baño: usar cáustica, cianuro de sodio y óxido de zinc; o usar cáustica, cianuro de sodio y cianuro de zinc. El primero es laborioso, pero los costos de los materiales son bajos. Se debe tener precaución con esta opción ya que la reacción es altamente exotérmica (más de 250 °F). La segunda opción tiene costos de materiales más elevados, pero requiere menos mano de obra y es más rápida.
Pasos del proceso. Para evitar la contaminación del baño de galvanoplastia, se prefiere la limpieza alcalina en remojo, seguida de una limpieza electrolítica. Si las piezas no están completamente limpias, el baño de galvanoplastia las limpiará, por lo que un mantenimiento más limpio no es tan crítico como con otros procesos de galvanoplastia. La limpieza debe ser sucedida por un decapado en ácido clorhídrico (20-30 por ciento) a temperatura ambiente, o en ácido sulfúrico (5-15 por ciento) a 105-120 °F (40-50 °C) para activar, desescamar, etc., piezas de acero antes de la galvanoplastia. Es preferible decapar las partes rechazadas fuera de línea para evitar la introducción de contaminación por cromo y para extender la vida útil del ácido. Las piezas se deberían decapar en la línea sólo si es necesario. Los aditivos de ácido y/o sales de fluoruro patentadas pueden ser beneficiosas en la limpieza y activación de las partes, así como en el aumento de la vida del ácido.
Los recubrimientos de cromato o pasivado y los topcoats son los tratamientos habituales posteriores a la galvanoplastia para cualquier depósito de zinc. Los recubrimientos de conversión de cromato que pueden proporcionar hasta 500 horas hasta la formación de sal blanca están disponibles, al igual que una amplia variedad de pasivados en colores desde transparente a negro.
Equipos y parámetros de operación. Los tanques para galvanoplastia de zinc cianurado pueden estar hechos de acero con bajo contenido de carbono, polipropileno, PVC o acero revestido de caucho. Los tanques de acero con bajo contenido de carbono deben estar aislados del circuito eléctrico para evitar corrientes de fuga. Para la galvanoplastia de barril, se recomiendan rectificadores que funcionan entre 6 y 15 V, y entre 5 y 10 asf. El rango de trabajo para las operaciones de rack es de 3 a 9 V, y 10 a 40 asf.
La mayoría de los baños funcionan a ciertos rangos de temperaturas, pero se recomienda el uso de equipos de refrigeración; los equipos de calefacción pueden ser convenientes en climas más fríos. El acero es el material que se debe seleccionar para cualquier equipo en contacto con la solución de galvanoplastia. La agitación es opcional para las operaciones de zinc en rack.
Se prefieren los ánodos especiales de zinc de alto grado, pero algunos profesionales de acabados de superficie han usado grados más bajos con éxito moderado. Si se usan bolsas de ánodos para evitar la rugosidad, la parte superior de las bolsas debe permanecer por encima de la solución de galvanoplastia. Los ánodos de zinc solubles se prefieren más que los ánodos de acero típicos en el zinc alcalino. Esto minimiza la oxidación del cianuro en el ánodo.
Poder de cobertura, poder de penetración y eficiencia del baño. El poder de cobertura es la capacidad de un baño de galvanoplastia para depositar metal en un área profundamente hundida. El poder de penetración es la capacidad de un baño de galvanoplastia para depositar un espesor uniforme de metal en áreas de alta y baja densidad de corriente. El poder de penetración de un baño de cianuro es significativamente mejor que el de un baño de cloruro de zinc. La eficiencia de la galvanoplastia de los baños de cianuro de zinc varía mucho dependiendo de la química del baño, temperatura y corriente. La eficiencia puede variar del 40 al 85 por ciento, y también se ve afectada por la formación de carbonatos en el baño.
Propiedades del depósito. La ductilidad del depósito de zinc, la uniformidad y la receptividad del cromato de un baño de cianuro de zinc son mejores que las obtenidas con los baños de cloruro de zinc y, en algunos casos, son mejores que en un baño alcalino sin cianuro. El depósito no muestra escamas ni polvo de estrellas (pequeñas picaduras). Cuanto más brillante es el depósito de zinc, mayor es el nivel orgánico en el depósito, lo que hace que el depósito sea menos dúctil y más tensionado. Las partes más brillantes pueden verse mejor, pero su desempeño en otras áreas puede verse afectado. Esta observación es válida para todos los sistemas de galvanoplastia de zinc. La codeposición de hierro se minimiza en baños de cianuro. Esto le da una apariencia azul uniforme y consistente.
Zinc alcalino sin cianuro
En los antiguos sistemas de galvanoplastia alcalinos libres de cianuro, el cianuro se reemplazaba por agentes complejantes o quelantes, como gluconato de sodio, trietanolamina o aminas poliméricas. Los baños resultantes presentaban problemas, tanto con el tratamiento de residuos como con la codeposición de hierro. Una segunda generación de agentes orgánicos de adición eliminaba los agentes quelantes, pero tenía otros inconvenientes, como la formación retardada de burbujas. Los agentes quelantes aún se emplean en diversas formulaciones comercialmente disponibles. La codeposición resultante del hierro puede dificultar la obtención del acabado de cromato azul uniforme, deseado por muchos clientes.
La mayoría de los procesos disponibles han eliminado los problemas observados en las tecnologías alcalinas anteriores mediante el uso de una familia completamente nueva de productos de reacción orgánica. Los profesionales de acabados de superficie tienen la opción de emplear zinc alcalino sin cianuro de baja química (baño de bajo contenido en metal) o cianuro alcalino de alta química (baño con alto contenido de metal). Además, se han introducido baños a base de potasio que ofrecen velocidades de galvanoplastia mayores y mejores eficiencias. La principal ventaja del último desarrollo es la capacidad de revestir espesores extremadamente uniformes en todo el rango de densidad de corriente. Esto, combinado con la propiedad antiquemado mejorada de estos procesos, permite una mayor densidad de las piezas en los racks de galvanoplastia. El proceso resultante contribuye a una alta productividad.
Los requisitos operativos para los procesos de galvanoplastia alcalina sin cianuro son los siguientes:
- Realizar diariamente análisis del baño, pruebas de celdas Hull y otras pruebas de galvanoplastia. Los niveles consistentes de zinc son críticos.
- Analizar, mantener y descargar limpiadores y ácidos de manera regular.
- Realizar mantenimiento preventivo para reducir los problemas de producción y minimizar los costos.
- Instalar alimentadores automáticos para componentes líquidos, con el objeto de eliminar el error humano.
- Para solucionar problemas, seguir cuidadosamente las recomendaciones del proveedor.
Conformación del baño. Hay tres opciones disponibles para la conformación del baño: usar cáustica y óxido de zinc, emplear concentrado de zinc preparado, o usar ánodos de zinc y cáustica. La opción A es dispendiosa. Los costos del material son moderados. Se debe tener precaución porque la reacción es altamente exotérmica. Sin embargo, estas temperaturas altas no se pueden evitar porque se requieren para disolver el óxido de zinc. La opción B tiene costos de materiales más altos, pero requiere menos mano de obra y es la más rápida. La opción C es la menos costosa en general, pero implica una demora debida a la disolución del zinc, así como una posible electrólisis de baja densidad de corriente para eliminar las impurezas metálicas no deseadas. También se podría requerir un mayor uso de purificadores.
Pasos del proceso. La limpieza y el decapado químico como se describió anteriormente para los procesos de zinc con cianuro alcalino, activan y preparan las piezas de acero para la galvanoplastia. Después de la galvanoplastia, los recubrimientos de conversión de cromato hexavalente y trivalente pueden proporcionar hasta 500 horas hasta la formación de sal blanca, según ASTM B 117. El uso de pasivados trivalentes actualmente, excede ampliamente los productos hexavalentes, aunque los productos hexavalentes todavía están disponibles.
Igualmente, en este caso existe una fuerte presión regulatoria contra el cromo hexavalente carcinógeno, forzando a muchas compañías a especificar acabados trivalentes. Una amplia variedad de pasivados trivalentes puede ofrecer colores que incluyen el transparente, iridiscente/multicolor, amarillo y negro, junto con varios acabados coloreados. Estos pasivados se usan normalmente solos o con capas de acabado o sellantes, y proporcionan de 12 a 700 horas de protección a la corrosión por sal blanca. Los topcoats extienden la protección, brindan durabilidad adicional o proporcionan un coeficiente de fricción específico. Los pasivados de gama alta, combinados con las tecnologías de sellantes más recientes, pueden ofrecer números de corrosión blanca competitivos con algunos acabados de aleación.
Equipos. El tanque de galvanoplastia puede estar hecho de acero con bajo contenido en carbono, polipropileno, PVC o acero revestido de caucho. Se prefieren los tanques de acero con bajo contenido de carbono, pero éstos deben estar aislados del circuito eléctrico. Para operaciones de barril, se recomienda una potencia de 6 a 15 V a una densidad de 5 a 10 asf. Para operaciones en rack, de 3 a 9 V y 10 a 40 asf. La mayoría de los baños funcionan a una amplia gama de temperaturas, pero el equipo de enfriamiento es esencial y un equipo de calefacción puede ser necesario en climas más fríos. El acero es el material que se debe seleccionar para cualquier equipo en contacto con la solución de galvanoplastia.
Los filtros son esenciales para un proceso de zinc alcalino sin cianuro. Uno o dos cambios por hora de la solución de galvanoplastia son prácticos en la mayoría de las instalaciones que utilizan cartuchos de polipropileno y pantallas de 10 a 15 μm. Las pantallas de filtro de papel o de celulosa pueden ser atacadas por la alcalinidad del sistema y, por lo tanto, deben evitarse. Se recomienda el uso de un sistema de filtración que pueda contener carbono. La agitación mecánica es opcional para las operaciones en rack de zinc alcalino. Generalmente, no se recomienda la agitación con aire.
Los ánodos están idealmente hechos en acero de bajo carbono, perforados y tienen un espesor de 0.125 a 0.375 pulgadas. El acero más grueso tiene una capacidad de transporte de corriente más alta que el acero más delgado. Las canastas de titanio no son recomendables, debido a su alta resistividad. Asegúrese de que las canastas de acero con bajo contenido de carbono se llenen de manera adecuada, según las sugerencias del proveedor, cuando se usen ánodos de zinc. Los ganchos porta-ánodos de tipo filo de navaja hacen mejor contacto que otros diseños. El material de polipropileno se recomienda para bolsas de ánodo. Las bolsas de algodón serían atacadas por una alta alcalinidad y se disolverían en el baño de galvanoplastia.
Asegúrese de que la parte superior de las bolsas permanezca por encima de la solución de galvanoplastia para evitar la rugosidad. La relación de ánodo a cátodo debe ser de aproximadamente 1:1. El consumo de metal de zinc es de 2.7 lb/1,000 A/h con una eficiencia de galvanoplastia del 100 por ciento. Los baños de galvanoplastia pueden trabajar con una eficiencia de cátodo del 30 al 80 por ciento. Esto puede variar dependiendo de la concentración de zinc, la temperatura, la concentración de aditivos y los niveles de carbonato.
Un tanque de generación de zinc fuera de línea, cuyo volumen es del 10 al 20 por ciento del volumen del tanque de galvanoplastia, facilita el control de la concentración de zinc. El tanque de generación de zinc es un tanque de acero bajo en carbono con acero y zinc. Los ánodos de zinc se disuelven galvánicamente en el tanque de acero (se recomiendan ánodos de acero con bajo contenido de carbono en el tanque de galvanoplastia). La nueva tecnología disponible puede reducir el tamaño de los tanques auxiliares o eliminarlos. La Figura 1 muestra una vista general de la configuración del generador galvánico.
Poder de cobertura, poder de penetración y eficiencia del baño. El poder de penetración del baño alcalino es aproximadamente del 40 al 65 por ciento (celda Haring), dependiendo de la química del baño o del tipo de aditivos utilizados. Casi cualquier parte revestida en un baño de galvanoplastia alcalina tendrá depósitos más gruesos en las áreas de baja densidad de corriente, en comparación con el cloruro de zinc. La eficiencia del baño del zinc alcalino sin cianuro disminuye con la densidad de corriente. Se puede lograr una mayor eficiencia con mayores concentraciones de zinc y temperaturas más altas. La formación de carbonato de sodio retardará la eficiencia de la galvanoplastia. Una rutina de eliminación de carbonato, generalmente por congelación, ayudará a mantener la eficiencia óptima del baño.
Propiedades del depósito. La ductilidad del depósito de zinc, la uniformidad del espesor y la receptividad del cromato en un baño alcalino sin cianuro, son mejores que la obtenida con los baños de cloruro de zinc. A diferencia de este último, el baño alcalino no presenta escamado ni polvo de estrellas cuando se opera correctamente. Cuanto más brillante sea el depósito de zinc, mayor será la oclusión de sustancias orgánicas en el depósito. Esto hace que el depósito sea menos dúctil y altamente tensionado.
Galvanoplastia de cloruro de zinc
Los procesos de galvanoplastia de cloruro de zinc han estado disponibles durante más de 40 años y han cambiado considerablemente durante este periodo. Han evolucionado desde procesos muy sensibles a la química del baño, temperatura, densidad de corriente, etc., a procesos que pueden trabajar en una amplia gama de condiciones. Ahora se encuentran disponibles procesos de alta temperatura que permiten densidades de corriente extremadamente altas para un rendimiento máximo.
Ventajas. Los procesos de cloruro ofrecen tres ventajas importantes sobre los sistemas alcalinos:
- Brillo y nivelación superiores, rivalizando con el de níquel-cromo.
- Eficiencias de galvanoplastia de 95 a 100 por ciento.
- No hay formación de carbonato, lo que permite una velocidad de galvanoplastia constante.
- Posibilidad de revestir sustratos como el hierro fundido y, lo que es más importante, aceros endurecidos utilizando una amplia variedad de métodos.
- Se puede lograr un excelente poder de cobertura. En condiciones controladas, superará con creces el proceso alcalino.
Desventajas. Desafortunadamente, asociadas a estas ventajas hay dos desventajas mayores:
- Las soluciones son corrosivas y, por lo tanto, más costosas, debido a la necesidad de equipos resistentes a la corrosión.
- El poder de penetración de los sistemas es muy ajustado, lo que trae como resultado una mala distribución del revestimiento. Se puede producir una acumulación significativa de espesor en las áreas de alta densidad de corriente (HCD, en inglés), también conocida como “dogboning”.
Las tres químicas de baño de cloruro de zinc para galvanoplastia, utilizadas más comúnmente, se muestran en la Tabla II.
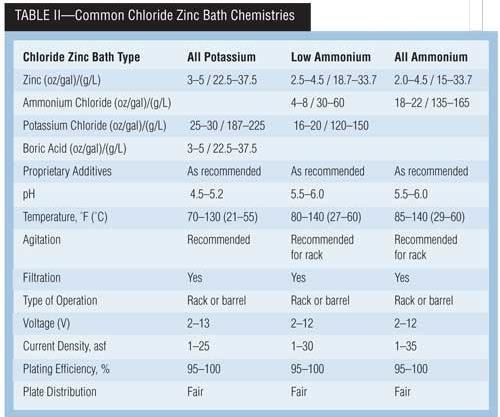
Tabla II. Químicas de baño de cloruro de zinc para galvanoplastia.
Requisitos de operación. Los requisitos sugeridos para una operación de galvanoplastia de cloruro de zinc sin problemas incluyen el monitoreo y ajuste del pH con la mayor frecuencia posible, al menos cada dos horas. El baño debe analizarse una vez por turno o al menos una vez al día, y los limpiadores y ácidos deben analizarse, mantenerse y desecharse de forma regular. El mantenimiento preventivo puede reducir los problemas de producción y minimizar los costos, mientras que los alimentadores automáticos para componentes líquidos eliminan los errores humanos y aseguran un rendimiento operativo constante.
Conformación del baño. Independientemente de la química del baño, el cloruro de zinc es la fuente de zinc en el baño y está disponible en líquido o sólido. El cloruro de zinc normalmente sólo se utiliza para la conformación del baño. Es importante que el cloruro de zinc esté libre —o lo más libre posible— de plomo. La presencia de plomo en el baño dará como resultado un depósito muy opaco, oscuro y sin refinar, y requiere hacer “dummying” (galvanoplastia para limpieza selectiva) con el objeto de eliminar el plomo del baño.
El cloruro de potasio brinda conductividad a la solución. Se prefiere la forma no tratada de cloruro de potasio. Varios agentes antiaglomerantes utilizados comúnmente pueden ser perjudiciales para el baño y deben evitarse. El cloruro de amonio sirve para varios propósitos: suministra conductividad y actúa como un complejante para el zinc. Los baños que usan cloruro de amonio, en general, tienen una ventana de operación más amplia y, por lo tanto, son más fáciles de controlar, principalmente debido a una mayor tolerancia a la contaminación por hierro, hasta tres veces más que la mayoría de los baños de ácido bórico. Los baños a base de cloruro de amonio también representan un problema potencial de manejo de desechos. Si no se separan los vapores de níquel o de cobre, el amoníaco podría dificultar la eliminación del níquel o el cobre. En algunas zonas, la descarga de amoníaco también está restringida.
Otros posibles constituyentes del baño incluyen: ácido bórico, utilizado sólo en sistemas sin amoníaco para ofrecer una acción amortiguadora; aditivos patentados para el refinamiento y abrillantado; peróxido de hidrógeno para tratar el baño de hierro y algunos contaminantes; y permanganato de potasio, el cual se usa de manera muy similar al peróxido de hidrógeno. Para operaciones en rack, este material sólo debe agregarse durante el tiempo de inactividad.
Pasos del proceso. Las piezas deben limpiarse y decaparse siguiendo los pasos descritos anteriormente para los procesos de zinc alcalino. Después de la galvanoplastia, el mismo surtido de cromatos y capas finales está disponible, como en el caso de la galvanoplastia de zinc alcalina. Algunos cromatos pueden ser más difíciles de usar en los acabados de cloruro de zinc completamente brillantes. Además, la contaminación por hierro puede dar lugar a una codeposición de hierro en áreas de alta densidad de corriente, causando la decoloración del acabado. La eliminación de esto requiere típicamente tratamientos de oxidación para el hierro.
Equipos y parámetros de operación. Los tanques para galvanoplastia de cloruro de zinc pueden estar hechos de polipropileno, PVC, fibra de vidrio o acero revestido. Todos deben ser filtrados antes de su uso. Para operaciones de barril, se recomienda 4-12 V a una densidad de 3-10 asf. Para operaciones en rack, 3-9 V a 10-40 asf. La mayoría de los baños trabajan en un rango amplio de temperaturas, pero el enfriamiento es esencial, y se pueden necesitar equipos de calefacción en climas más fríos. Cualquier equipo que entre en contacto con la solución de recubrimiento debe ser fabricado con materiales resistentes a la corrosión.
Los filtros también son esenciales, operados a uno o dos cambios por hora de la solución de galvanoplastia, utilizando cartuchos de polipropileno o filtros de placa capaces de filtrar de 10 a 25 μm. Se requiere agitación uniforme del aire para las operaciones de rack. Se deben usar ánodos especiales de zinc de alta calidad, y canastas de titanio con ánodos de bloque o de bola, como bloques de canasta colgando de los ganchos. Para los procesos de rack, se recomienda polipropileno o algodón para las bolsas de ánodo y se prefiere el polipropileno motoso. El tejido de la bolsa no debe estar demasiado apretado, ya que esto podría hacer que las bolsas se tapen prematuramente. Asegúrese de que la parte superior de las bolsas permanezca por encima de la solución de galvanoplastia para evitar la rugosidad.
Poder de cobertura, poder de penetración y eficiencia del baño. Los depósitos de cloruro de zinc tienen un excelente poder de cobertura, pero un pobre poder de penetración. Un baño de galvanoplastia de cloruro puede revestir más profundamente en el interior de un tubo que un baño alcalino sin cianuro. Sin embargo, la distribución del espesor del depósito es más pobre. La nueva tecnología ha permitido que los sistemas de cloruro de zinc se enlacen con una distribución mejorada, una mejor receptividad del recubrimiento de conversión y sin polvo de estrellas, al mismo tiempo que mantienen todas las propiedades del depósito de cloruro de zinc, incluida su deposición laminar.
Propiedades del depósito. Los depósitos de cloruro de zinc de los baños que operan en condiciones normales son completamente brillantes, con muy buena nivelación y con ductilidad, uniformidad y receptividad de cromato aceptables. Los depósitos, en particular los de procesos de galvanoplastia en barril o donde se alterna mucho entre contacto y no contacto, mostrarán escamas o polvo de estrellas. Un alto nivel de abrillantador o de orgánicos también pueden hacer que el depósito sea menos receptivo a los cromatos, lo cual resultará en una apariencia inaceptable y bajo rendimiento de corrosión.
Galvanoplastia de aleación de zinc
La galvanoplastia de aleación de zinc, sin incluir el latón, no recibió un reconocimiento significativo hasta principios de los años ochenta. Desde entonces, la gama de aleaciones ha aumentado y los procesos de producción se han refinado considerablemente. En los últimos 20 años, estos procesos han ganado una amplia aceptación comercial. Esto se debe al impulso de varias industrias que buscan reemplazar el cadmio o simplemente aumentar el desempeño contra la corrosión más allá de las capacidades de la galvanoplastia. La industria automotriz fue una fuerza impulsora clave, ya que los fabricantes de automóviles buscaron extender las garantías y reducir las reclamaciones por garantía.
Los baños de aleación de zinc disponibles en la actualidad son capaces de satisfacer ambas necesidades, produciendo depósitos que brindan una mejor protección contra la corrosión y una mayor lubricidad, ductilidad y dureza.
Procesos disponibles. Hay una serie de procesos de aleación de zinc disponibles comercialmente. Revisaremos el zinc-níquel (Zn/Ni), el zinc-cobalto (Zn/Co), el zinc-hierro (Zn/Fe) y el estaño-zinc (Sn/Zn).
La Tabla III enumera las diferentes composiciones de aleaciones y sus procesos asociados.
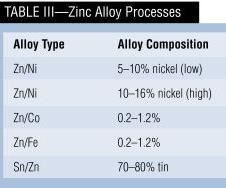
Tabla III. Procesos de aleación de zinc.
Los procesos de galvanoplastia para las aleaciones de hierro y cobalto tienen sistemas aditivos similares a sus equivalentes no aleados, puesto que se utilizan bajas concentraciones de aleación en estos procesos. Los sistemas Zn/Ni, sin embargo, requieren procesos que son bastante diferentes de sus equivalentes no aleados.
Se ha convertido en la alternativa más popular al zinc y a las otras aleaciones, debido a su alta protección contra la corrosión y su alta tolerancia al calor cuando se revisten altas aleaciones, con variación entre el 12 y el 16 por ciento de níquel. Este depósito de alta aleación mantiene la mayoría de su protección contra la corrosión a temperaturas elevadas y proporciona una mayor resistencia al desgaste.
Los depósitos de aleación de zinc-níquel se pueden producir mediante un proceso alcalino o de cloruro. El zinc-níquel alcalino tiene un costo de operación más alto que el zinc-níquel ácido, principalmente debido a la falta de ánodos de níquel solubles en el sistema alcalino. Éstos no son posibles en los sistemas alcalinos.
El proceso de galvanoplastia alcalina ofrece una buena distribución del revestimiento, pero tiene una eficiencia muy baja. Los complejantes utilizados pueden afectar negativamente al tratamiento de residuos. El zinc y el níquel se reponen utilizando ánodos de zinc o un generador de zinc galvánico. El generador galvánico utiliza ánodos insolubles, comúnmente de níquel o níquel revestido. La fuente de níquel es generalmente un concentrado de níquel líquido agregado por amp-hora.
Se han desarrollado nuevas tecnologías en sistemas de aleación de cloruro de zinc-níquel que tienen propiedades de distribución de la aleación casi tan uniformes como el níquel zinc alcalino. La reposición de metal de los baños de cloruro de zinc níquel puede hacerse por uno de los dos siguientes métodos: 1) rectificador simple con ánodos de zinc, y sales de níquel alimentadas por amp-hora o 2) ánodos de zinc y níquel en rectificadores separados. Se prefiere la configuración del rectificador dual para un mejor control de la aleación y un menor costo de operación de los ánodos de níquel sobre las sales. Las configuraciones de un solo rectificador también conducirán a un crecimiento acelerado del zinc en las operaciones de rack, lo que provoca una dilución innecesaria del baño.
La de estaño-zinc es más una aleación de estaño que de zinc, ya que el estaño está presente en el depósito en un 70 a 75 por ciento, y el zinc está presente en 25 a 30 por ciento. Mientras que el baño de aleación de estaño-zinc está revestido con fórmulas de baño tanto ácidas como alcalinas, los más fáciles de usar generalmente se colocan en un rango de pH casi neutro, de 6.0 a 7.0. Los ánodos utilizados suelen ser de 75/25 estaño-zinc. La agitación del cátodo es obligatoria, y se especifica agitación “sin aire”. La alta concentración de estaño en el depósito resulta en un costo de acabado más alto que las otras aleaciones de zinc. La protección contra la corrosión es similar a la de las aleaciones de zinc-níquel. La aleación de estaño-zinc tiene buenas propiedades eléctricas y una ductilidad excepcional, lo que la hace ideal para fabricación posterior a la galvanoplastia. El estaño también es un metal no regulado, y como tal, cualquier desecho generado en el proceso generalmente se elimina como no peligroso.
Zinc-cobalto. Los sistemas alcalinos para la galvanoplastia de aleaciones de zinc-cobalto son fáciles y económicos de operar y producen un depósito con una aleación y una uniformidad de espesor excepcionales. Al igual que en el proceso de aleación de níquel alcalino, no es extraño que en realidad se aplique una aleación triple de zinc-cobalto-hierro, debido a la presencia de complejantes. Se prefiere el proceso de galvanoplastia alcalina, pero el sistema de cloruro se puede usar donde sea necesario revestir piezas de metal endurecido o de fundición.
Los depósitos de zinc-hierro se producen actualmente utilizando sólo un proceso alcalino sin cianuro. Los procesos de cloruros para producir aleaciones de Zn/Fe aún no se utilizan ampliamente en el mercado. Los baños de Zn/Fe son los sistemas de aleación de zinc más económicos y fáciles de operar. El depósito tiene muy buena resistencia a la corrosión, ductilidad y soldabilidad. Los depósitos de aleación de hierro tienen un aspecto negativo: pierden una protección sustancial contra la corrosión cuando se exponen a temperaturas elevadas. Por lo tanto, no se recomienda su uso a temperaturas superiores a 200°F.
Elegir el proceso adecuado de aleación de zinc. Sólo hay dos cosas por definir. La primera es el tipo de aleación requerida. La segunda, en el caso de las aleaciones de níquel y cobalto, es decidir si usar un baño de galvanoplastia alcalina o de cloruro. La primera opción es fácil, ya que esto generalmente se detalla en las especificaciones del cliente. La elección de los tipos de baño puede ser un poco más complicada. Hay varias consideraciones:
- Algunos sustratos, como la fundición de hierro o las partes endurecidas o con carbonitruro, requieren baños de tipo cloruro para ser revestidos correctamente. La iniciación consistente de la galvanoplastia puede ser difícil al usar los baños alcalinos en estos sustratos.
- Los baños de cloruro requieren el uso de equipos resistentes a la corrosión. Los baños de aleación alcalina contienen complejantes que también pueden ser corrosivos para los equipos. Dependiendo de la aleación del baño y de los complejantes utilizados, puede ser necesario usar equipos más resistentes a la corrosión que los que se necesitarían para un baño de zinc alcalino normal.
- En el caso de las aleaciones de níquel, pueden ser necesarias modificaciones del tratamiento de residuos, para manejar el níquel y los niveles altos de complejantes fuertes.
Topcoats y selladores. Debido al contenido de aleación del depósito, se requieren formulaciones de pasivado especiales para cada uno de los diferentes depósitos de aleación. Actualmente existen cromatos hexavalentes y trivalentes disponibles en una gama de colores para la mayoría de las aleaciones de zinc. Sin un recubrimiento de conversión de pasivado, las características de corrosión de las aleaciones de hierro y cobalto no son significativamente diferentes a las del zinc puro. En el caso de las aleaciones de níquel, sin pasivados, el inicio de la corrosión de sal blanca es aproximadamente el mismo que para el zinc puro, pero la progresión de la corrosión se reduce significativamente, especialmente al aumentar el contenido de níquel.
Las capas de pasivado tienden a concentrar el componente de aleación dentro de la capa de conversión, dando como resultado una mejor protección sobre el zinc tratado. Las formulaciones de cromato y los parámetros para las aleaciones son significativamente diferentes de los que se usan para el zinc. También es destacable que las propiedades de fricción de estas aleaciones pueden ser muy diferentes a las del zinc. El zinc-estaño tiene valores de Coeficiente de Fricción (CoF, en inglés) más bajos, mientras que el zinc-níquel tiene valores más elevados. Esto requerirá formulaciones de topcoat modificadas en comparación con el zinc, para cumplir con los requisitos de CoF especificados por los fabricantes.
Editado por Matt Stauffer.
CONTENIDO RELACIONADO
-
La mexicana AMINSA estrena nueva línea de cromo totalmente automatizada en Aguascalientes
AMINSA, empresa de origen mexicano, está estrenando en Aguascalientes una línea 100% automatizada para acabados en cromo, la cual fue diseñada para servir a la industria automotriz.
-
Por publicarse nueva NOM 001 sobre descargas de aguas residuales: Semarnat
Este instrumento no se había actualizado en las últimas dos décadas y media, a pesar de que las Normas se deben actualizar cada cinco años.
-
Una plática con Manuel Álvarez Bermejillo, fundador de Galvanizadora de Occidente
En 1964, con apenas 21 años, Manuel Álvarez Bermejillo fundó la empresa Galvanizadora de Occidente. Aquí la entrevista que tuvimos con él.